Understanding Micro Precision Injection Molding in Today's Manufacturing Landscape
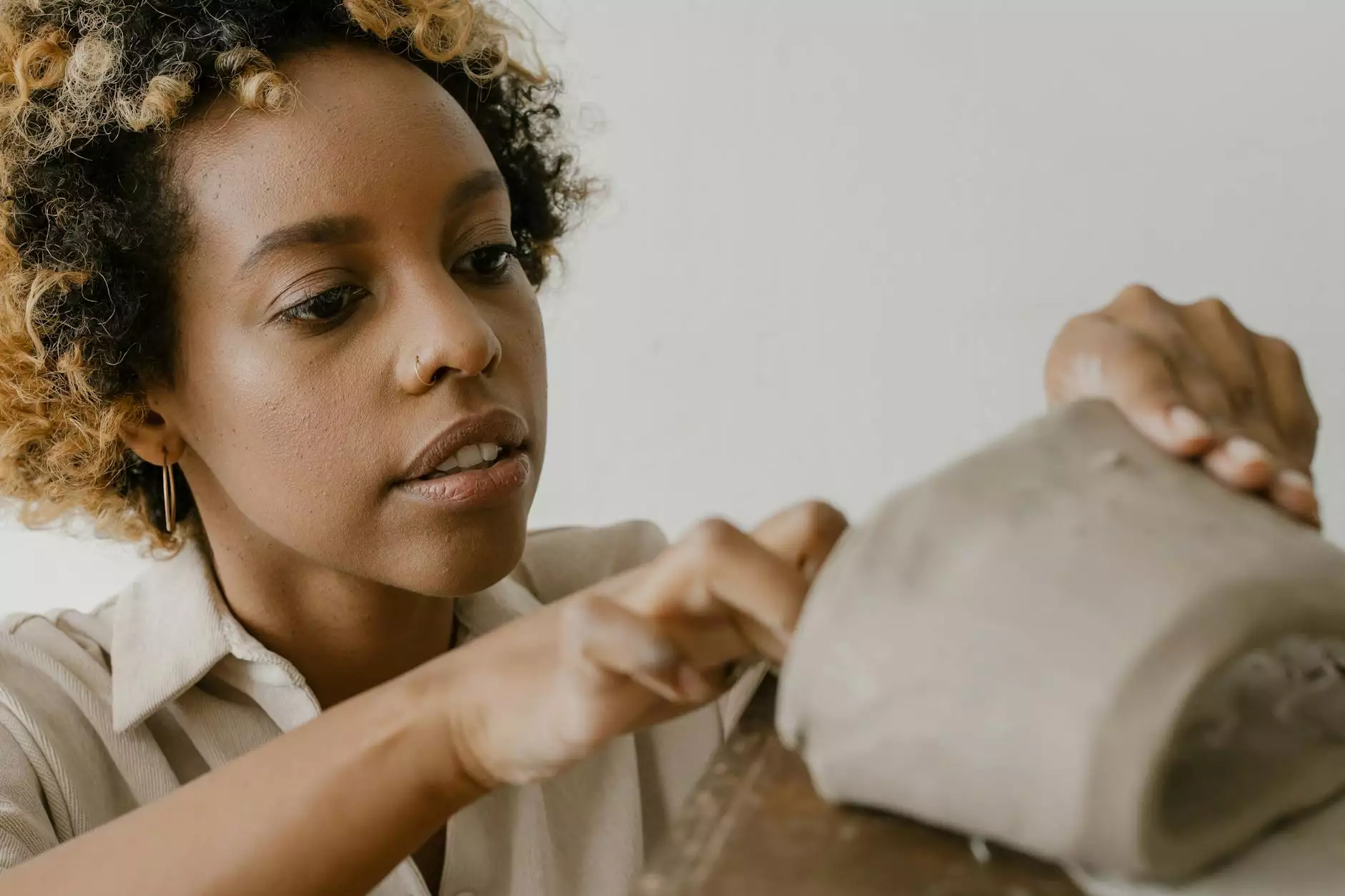
Micro precision injection molding is a revolutionary process that has transformed the landscape of modern manufacturing. As industries strive for greater efficiency and precision, this technology emerges as a cornerstone in the production of high-quality components. In this article, we will delve into the specifics of micro precision injection molding, its benefits, and its applications in the metal fabrication sector.
The Process of Micro Precision Injection Molding
The process of micro precision injection molding involves the injection of molten material into a precisely designed mold. The ability to control temperatures and pressures allows manufacturers to create highly detailed and intricate parts with exceptional accuracy. Here’s a breakdown of the steps involved:
- Mold Design: The journey begins with an expertly crafted mold designed to meet the specific requirements for the end product.
- Material Selection: Selecting the right material is crucial. Thermoplastics and thermosetting polymers are commonly used due to their versatility.
- Injection: The molten material is injected into the mold cavity at high pressure, allowing it to fill all intricate details.
- Cooling: Once the mold is filled, the material cools and solidifies, taking on the shape of the mold.
- Demolding: Finally, the solidified part is removed from the mold, ready for further processing or finishing.
Key Advantages of Micro Precision Injection Molding
Why has micro precision injection molding become a preferred technique in metal fabrication and other industries? Here are some compelling benefits:
- Enhanced Precision: The process allows for the production of components with tolerances as narrow as a few microns, delivering exceptional detail.
- Reduced Material Waste: High precision means less scrap material is produced, making it an environmentally friendly choice.
- Scalability: Once a mold is crafted, it can be utilized for large-scale production, significantly lowering unit costs.
- Complex Parts Creation: The ability to produce intricate designs and complex geometries is unparalleled in traditional manufacturing techniques.
- Fast Turnaround Times: With rapid prototyping capabilities, businesses can accelerate their product development cycles.
Applications of Micro Precision Injection Molding in Metal Fabrication
The application of micro precision injection molding is vast and varies across industries. In the realm of metal fabrication, it plays a pivotal role in several key areas:
1. Medical Devices
In the medical industry, precision is paramount. From tiny components in surgical instruments to intricate parts of diagnostic equipment, micro precision injection molding ensures that every piece is manufactured to the highest standards. This technology enables the creation of bio-compatible materials that meet stringent regulatory requirements.
2. Electronics
The electronics industry benefits immensely from this technology. Components like connectors, housings, and insulation parts can be produced at a micro-level, ensuring compatibility and performance while optimizing weight and size.
3. Aerospace Engineering
The aerospace sector demands components that can withstand extreme conditions. Using micro precision injection molding, manufacturers can produce lightweight yet strong parts that conform to rigorous safety and performance standards.
4. Automotive Industry
Modern vehicles require numerous small components for functionality and safety. Micro precision parts can improve the efficiency of engines, enhance electrical systems, and reduce emissions—making them an integral part of contemporary automotive engineering.
Choosing the Right Partner for Micro Precision Injection Molding
When it comes to investing in micro precision injection molding, it is essential to collaborate with experts who understand both the technology and the specific industry needs. At DeepMould.net, we pride ourselves on our expertise in metal fabrication and our commitment to quality. Here’s what to look for in a partner:
- Experience: Ensure your partner has a proven track record in micro precision injection molding.
- Capabilities: Assess their technology and equipment to handle complex designs and high-volume production.
- Quality Assurance: A partner should have stringent quality control processes to ensure every component meets necessary standards.
- Communication: Effective collaboration is vital; choose a partner that values transparency and communication throughout the project.
The Future of Micro Precision Injection Molding
The advancement of micro precision injection molding continues to evolve with technology. Innovations in materials, automation, and digital manufacturing will only enhance the capabilities of this process. Furthermore, the integration of artificial intelligence and machine learning can optimize production efficiency, predictive maintenance, and quality control, further positioning this technique at the forefront of metal fabrication.
Conclusion: Embracing the Micro Precision Revolution
In summary, micro precision injection molding serves as a vital technology in various sectors, particularly in metal fabrication. Its ability to produce highly precise and complex components with reduced waste and faster turnaround times positions it as a game-changer in manufacturing. As industries evolve, embracing this technology will be crucial for businesses looking to enhance their production capabilities and remain competitive.
For those seeking a trusted partner in micro precision injection molding, DeepMould.net stands ready to deliver innovative solutions tailored to your specific needs. Let us help you forge your path in the burgeoning world of precision-driven manufacturing!