Understanding Plastic Mold Fabrication: The Backbone of Modern Manufacturing
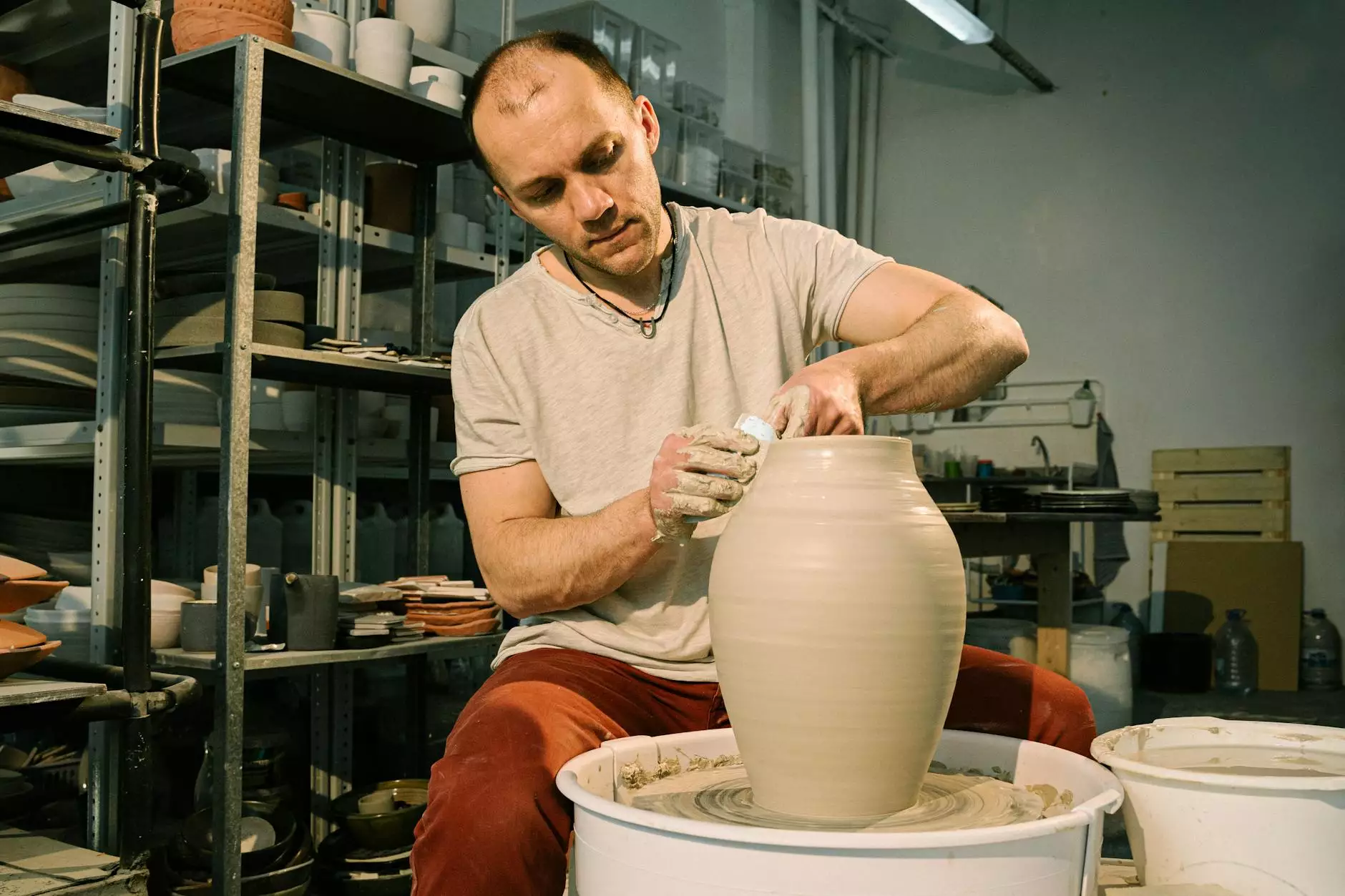
The process of plastic mold fabrication is one of the most crucial aspects of modern manufacturing. It plays a vital role in various industries, including automotive, consumer goods, and electronics. As we delve into this intricate world, we will uncover the techniques, benefits, and innovations that make plastic mold fabrication an essential component of production today.
1. What is Plastic Mold Fabrication?
Plastic mold fabrication refers to the process of designing, manufacturing, and refining molds used for producing plastic products. This process encompasses various stages, from initial design to final production, and involves the following key components:
- Design: Utilizing CAD (Computer-Aided Design) software to create precise mold designs.
- Machining: Fabricating molds from various materials, typically metal, to ensure durability and precision.
- Assembly: Putting together different parts of the mold to form a complete unit.
- Testing: Conducting trials to ensure that the molds operate correctly and produce the desired product quality.
- Production: Using these molds to mass-produce plastic components for various applications.
2. The Importance of Plastic Mold Making
In today's fast-paced world, businesses must focus on efficiency, quality, and innovation. Plastic mold making serves as an anchor for these goals. Here’s why:
2.1 Cost-Effectiveness
Custom molds can significantly reduce production costs, especially for high-volume manufacturing. Plastic mold fabrication allows companies to produce large quantities of uniform products at a lower per-unit cost compared to other manufacturing methods.
2.2 Enhanced Product Quality
Precision in mold design results in higher quality products. Well-fabricated molds ensure minimal defects during the manufacturing process, leading to better consumer satisfaction and durability of the finished products.
2.3 Flexibility and Customization
The ability to create custom molds means businesses can adapt quickly to market demands. Whether it is a unique product design or a new feature, plastic mold fabrication allows for rapid adjustments to meet customer needs.
3. The Process of Plastic Mold Fabrication
Let’s delve deeper into the steps involved in plastic mold fabrication. Each stage is critical to ensuring the final product meets industry standards and customer expectations.
3.1 Concept and Design
Every successful plastic component begins with a concept. Designers work closely with engineers to develop a mold that meets specific requirements using:
- 3D Modeling Software: To visualize the mold before it is manufactured.
- Material Selection: Choosing the right materials based on the final product's requirements.
3.2 Prototyping
Before moving to production, a prototype of the mold is created. This step allows manufacturers to test the design and make necessary adjustments. Rapid prototyping techniques, such as 3D printing, are often used to create these initial molds quickly.
3.3 Machining the Mold
Once the design is finalized, the actual mold is machined from materials like steel or aluminum. This step includes:
- CNC Machining: Utilizing computer-controlled machines for high precision.
- EDM (Electrical Discharge Machining): A method used to shape complex mold geometries that can’t be achieved through standard machining.
3.4 Mold Assembly
In this phase, all the machined components are assembled into a complete mold. This includes carefully aligning and securing the movable parts to ensure they function seamlessly during production.
3.5 Testing and Quality Control
Quality control is paramount in plastic mold fabrication. Molds are subjected to rigorous testing to ensure they meet durability and precision standards. This may involve:
- Trial Runs: Testing the mold with actual production materials.
- Dimensional Inspection: Ensuring that all measurements are accurate and within tolerances.
4. Types of Plastic Molds
Different types of molds are used for various applications. Understanding these mold types can help businesses choose the right one for their needs:
4.1 Injection Molds
Injection molds are widely used in high-volume production. In this process, melted plastic is injected into the mold cavity, where it cools and solidifies into the final product.
4.2 Blow Molds
Blow molding is especially useful for creating hollow objects. This method involves inflating a hot plastic tube inside a mold to form containers, bottles, and other hollow structures.
4.3 Compression Molds
Compression molds are used for making large parts. In this method, preheated plastic material is placed into a mold cavity and compressed to create the shape.
4.4 Rotational Molds
Rotational molding involves heating a plastic material inside a mold that rotates around two axes, allowing the material to coat the interior of the mold evenly.
5. Innovations in Plastic Mold Fabrication
The field of plastic mold fabrication is constantly evolving, with new technologies and methods emerging that enhance production capabilities and outcomes.
5.1 Additive Manufacturing
3D printing has revolutionized mold making by allowing for rapid prototyping and even the production of molds directly from 3D models. This innovation allows for quick iterations and significant reductions in lead times.
5.2 Advanced Materials
New composite materials provide greater durability and flexibility for molds. Using innovative materials can lead to longer-lasting molds that withstand the rigors of production better than traditional steel molds.
5.3 Automation and Smart Technology
Automation in the production of molds has led to increased efficiency and precision. Smart technologies, including IoT devices, allow for real-time monitoring of mold conditions and quick adjustments to maintain quality standards.
6. Benefits of Partnering with a Top Plastic Mold Manufacturer
When businesses choose to work with a reputable plastic mold manufacturer such as Hanking Mould, they gain access to a wealth of benefits:
6.1 Expert Knowledge and Experience
Established manufacturers possess extensive knowledge of plastic mold fabrication techniques, ensuring that clients receive the highest quality products.
6.2 Customized Solutions
Custom solutions provided by expert mold manufacturers can significantly enhance product development. Tailored molds meet specific requirements that off-the-shelf solutions just can't satisfy.
6.3 Proactive Support and Consultation
Leading manufacturers offer ongoing support throughout the design and production processes, ensuring that the end product aligns with the client’s vision and market needs.
7. Conclusion
In conclusion, plastic mold fabrication is a cornerstone of modern manufacturing, enabling the production of high-quality plastic products across diverse industries. With innovations continually shaping the landscape of mold making, businesses will not only enhance efficiency but also meet the ever-evolving demands of the market.
Partnering with a top-tier manufacturer like Hanking Mould can make all the difference in achieving competitive advantages through superior plastic products. As you consider your options, remember the significant benefits that an investment in quality and expertise brings to your operations.
For more information about our services in plastic mold fabrication, visit hanking-mould.com