The Essential Role of Car Parts Mold in Automotive Manufacturing
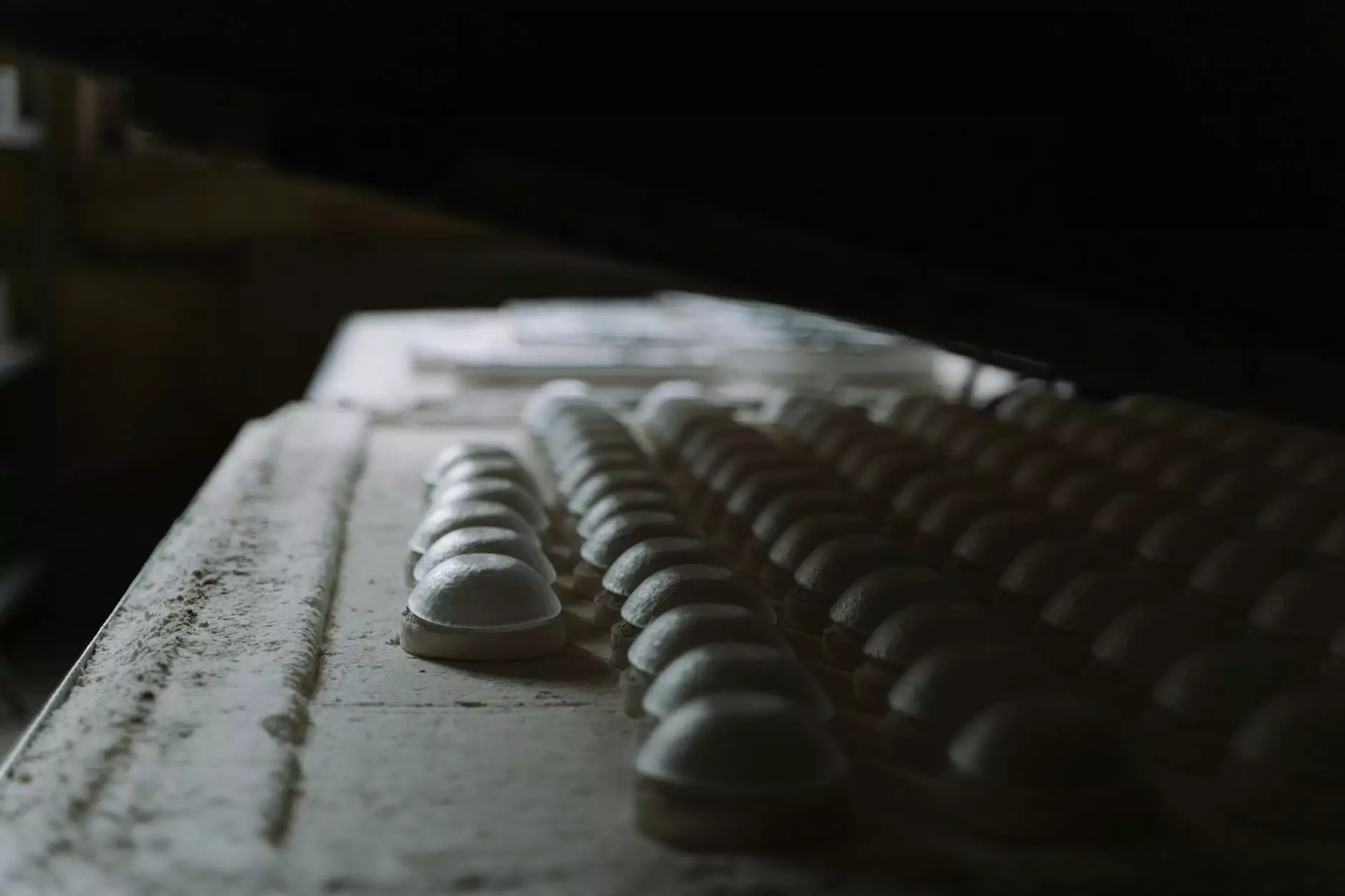
In today's fast-paced automotive industry, the production of car parts mold stands at the forefront of innovative manufacturing. As cars become more advanced, the demand for high-quality parts molds increases, ensuring that vehicles are not only functional but also efficient and reliable. This article delves into the significance, processes, and advancements in car parts molding, providing comprehensive insight into this key aspect of automotive manufacturing.
Understanding Car Parts Mold
A car parts mold is a tool used to form car components through processes such as injection molding, blow molding, or compression molding. These molds define the shape and dimensions of automotive parts, ranging from interior elements like dashboards to critical external components such as bumpers and fenders. The precision of these molds is vital for maintaining the performance and safety of the vehicle.
The Importance of Molds in Automotive Manufacturing
- Precision Manufacturing: Molds enable high levels of accuracy in the creation of complex geometries.
- Cost Efficiency: Utilizing molds in mass production significantly reduces the costs associated with machining and manual labor.
- Material Versatility: Molds can be crafted from a variety of materials, allowing for the production of parts that are strong, lightweight, and resistant to environmental damage.
Types of Molding Processes for Car Parts
There are several key molding processes used in creating car parts molds, each with unique advantages and applications:
1. Injection Molding
This is the most widely used method in automotive manufacturing, particularly for plastic components. It involves injecting molten material into a pre-designed mold. The benefits of injection molding include:
- High Efficiency: Capable of producing thousands of parts in a short time frame.
- Complex Designs: Facilitates intricate designs that would be difficult or impossible to achieve with other methods.
- Minimal Waste: Material is precisely used, reducing scrap and contributing to sustainable practices.
2. Blow Molding
Blow molding is ideal for producing hollow parts, such as fuel tanks or air ducts, by inflating hot plastic to fit into a mold. This process ensures:
- Lightweight Components: Parts produced are often lighter, improving fuel efficiency.
- Consistent Wall Thickness: Offers uniformity in the structure of the part.
3. Compression Molding
This process involves placing a pre-measured amount of material into a heated mold and applying pressure. It is suitable for thermosetting plastics and provides:
- Durability: The final products are highly resistant to impact and thermal deformation.
- Cost-Effectiveness for Short Runs: Ideal for smaller production runs due to its lower initial costs.
The Materials Used in Car Parts Molds
Choosing the right material for a car parts mold is essential for ensuring the durability and effectiveness of the manufacturing process. Common materials used include:
1. Steel
Steel molds are favored for their strength and durability. They are capable of withstanding high pressures and temperatures, making them suitable for high-volume production.
2. Aluminum
Aluminum molds are lightweight and offer great thermal conductivity, resulting in faster cycle times. However, they are less durable than steel molds and are often used for lower production runs.
3. Mold Steel Alloys
Alloyed steels incorporate a blend of materials that enhance toughness and wear resistance, making them ideal for complex mold designs that require longevity under stress.
Benefits of High-Quality Car Parts Molds
Investing in high-quality car parts molds brings numerous advantages to manufacturers:
1. Improved Product Quality
High-quality molds lead to precision parts that meet strict automotive standards, reducing the likelihood of defects and recalls.
2. Increased Production Speed
Efficient mold designs enable quicker production cycles, helping manufacturers meet market demands without sacrificing quality.
3. Enhanced Safety
Reliable molds ensure that critical safety parts conform to specifications, thereby contributing to the overall safety of the vehicle.
Challenges in Car Parts Mold Manufacturing
Despite advances in technology, there are still challenges in the realm of car parts molds:
1. Rising Costs
As materials and labor costs increase, manufacturers must find ways to maintain profitability without compromising quality.
2. Technological Advancements
Keen competition drives the need for continuous investment in the latest molding technologies and equipment, making it essential for companies to adapt swiftly.
The Future of Car Parts Molds in Manufacturing
The automotive industry is on the brink of significant transformation, largely driven by electric vehicle (EV) technologies and sustainability initiatives. Consequently, the future of car parts molds will also reflect these changes:
1. Adoption of Sustainable Materials
Manufacturers are increasingly exploring biodegradable and recyclable materials for molds to align with sustainability goals.
2. Integration of Smart Manufacturing
Industry 4.0 technologies, like IoT, are being incorporated into mold manufacturing processes to enhance efficiency and predict maintenance needs.
3. Customization and Flexibility
As consumer demands shift towards personalized vehicles, molds will need to adapt quickly to create custom car parts while maintaining efficiency in production.
Conclusion
In summary, the significance of car parts molds cannot be overstated in the automotive manufacturing process. They are essential for producing high-quality, precise automotive components efficiently and safely. As technology continues to evolve, so too will the methodologies and materials used in mold production, driving the industry toward a more sustainable and innovative future. Companies like deepmould.net are at the forefront of this evolution, delivering exceptional mold manufacturing solutions that empower the automotive sector.